Unlocking Creativity: How Math Powers Every Aspect of Fashion Design
Introduction: The Hidden Force Behind Every Garment
Fashion design is often celebrated for its creativity, flair, and trendsetting style. Yet beneath the artistry lies a foundation built on mathematics. From the earliest sketches to the final fitting, math enables designers to transform ideas into wearable works of art. Whether you’re an aspiring designer or simply curious about the industry, understanding how mathematics powers fashion will deepen your appreciation for every stitch and seam.

Source: pinterest.com
Precise Measurements: The Bedrock of Fit and Consistency
One of the most direct uses of math in fashion is ensuring accurate measurements. Designers rely on arithmetic and geometry to measure sample garments for fitting and to keep sizes consistent across collections. For example, when creating a wedding gown prototype, a designer must calculate the area of fabric needed, taking into account the union of smaller geometric shapes like triangles and rectangles. This ensures the correct amount of material is ordered, minimizing waste and cost [4] .
To replicate sizes accurately, designers must use standard size charts and apply mathematical formulas. For instance, if a designer is asked to scale a medium shirt pattern to a large, they may increase all linear measurements proportionally, using ratios and percentages to maintain fit and shape.
Pattern Making: Transforming 2D Shapes Into 3D Garments
Pattern making is a mathematical art. Designers map out two-dimensional shapes that, when sewn together, fit the three-dimensional curves of the human body. This process involves geometry, algebra, and spatial reasoning [1] . The pioneering work of mathematicians like Euler and Monge laid the groundwork for mapping curved surfaces, a technique still used today in pattern design.
For practical implementation, designers often use pattern-drafting software that integrates mathematical models. These tools allow the adjustment of darts, seams, and curves with precision. If you’re interested in learning pattern making, consider these steps:
- Study basic geometry and algebra (many online courses and textbooks are available).
- Practice creating patterns for simple garments (skirts, t-shirts) using measurement formulas.
- Experiment with digital pattern-making software to visualize how 2D patterns form 3D clothing.
Many fashion schools offer introductory courses in pattern drafting; you can search for programs at accredited institutions or explore online learning platforms specializing in design fundamentals.
Fabric Efficiency and Sustainable Design: The Math of Zero Waste
Mathematics plays a critical role in sustainable fashion design. By applying concepts from geometry and optimization, designers can reduce fabric waste and create eco-friendly garments. For example, zero-waste pattern cutting arranges pattern pieces like puzzle parts, maximizing material use and minimizing scraps [1] [2] .
To implement these techniques:
- Analyze standard fabric widths and plan pattern layouts to optimize yield.
- Use graph paper or digital tools to experiment with different arrangements.
- Study case studies of brands known for sustainable practices; many share their approaches through industry articles and interviews.
Advanced designers use mathematical algorithms to generate tessellations and fractal patterns, further pushing the boundaries of design and sustainability. The adoption of virtual try-on and 3D modeling also relies on mathematical simulations to reduce the need for physical samples, lowering carbon footprints.
Cost Control: Budgeting and Material Management
Every successful fashion line depends on effective cost management. Designers use math to calculate the total costs of materials, labor, and production. For example, if a dress requires two types of fabric at different prices, the designer must calculate the yardage needed for each and ensure the total falls within budget [5] .
To manage costs effectively:
- List all required materials and research current market prices.
- Create a spreadsheet to track expenses and compare suppliers.
- Factor in extra material for potential errors or alterations.
You can find templates and cost calculators on business resource websites for designers, or ask mentors and professionals for sample budgets when starting your own fashion projects.
Digital Innovation: Math in 3D Modeling and Virtual Design
With the growth of digital fashion, math is more essential than ever. Designers now use 3D modeling software to create virtual prototypes of garments, adjusting proportions and drape in a simulated environment before producing physical samples [3] . This not only saves time and resources but also allows for precise design testing and easier communication with manufacturers.
For those interested in digital fashion design:
- Explore beginner-friendly 3D modeling tools (such as Clo3D, Blender, or Marvelous Designer).
- Practice visualizing how flat patterns translate into 3D forms.
- Consider online tutorials, community forums, or collaborative projects to build your skills.
The use of data analysis is also on the rise: fashion brands analyze sales and trend data to forecast demand, make inventory decisions, and respond to consumer preferences. This data-driven approach enhances both creativity and profitability in a competitive market.

Source: pinterest.com
Trend Forecasting: The Math Behind Fashion’s Future
Fashion is not only about what looks good today, but also what will be popular tomorrow. Designers and retailers use mathematical models to analyze past sales, consumer behavior, and global trends [3] . Algorithms can predict which colors, cuts, or fabrics are likely to trend, enabling brands to make informed production and marketing decisions.
If you want to learn more about fashion forecasting:
- Research case studies from large retailers who use data analytics (many industry publications provide insights).
- Consider courses in business analytics or fashion merchandising.
- Join professional associations or online communities focused on fashion technology to stay updated on the latest tools.
Challenges and Alternatives: Navigating a Mathematical Mindset
Some aspiring designers may feel intimidated by the technical aspects of math in fashion. However, resources are widely available to help build these skills, from introductory math courses to specialized fashion math workshops. Collaboration with professionals-pattern makers, cost analysts, digital modelers-can also help bridge any gaps.
Alternative approaches include:
- Partnering with technical specialists for complex projects.
- Using intuitive design software with built-in mathematical calculations.
- Participating in design competitions or mentorship programs that emphasize practical applications of math.
Accessing Resources and Next Steps
If you’re eager to integrate math into your fashion journey, consider the following actionable steps:
- Enroll in basic math or geometry courses through accredited schools or online platforms.
- Reach out to local fashion schools or community colleges for beginner pattern-making classes.
- Connect with industry professionals at events, workshops, or through professional organizations.
- Utilize open educational resources, such as university extension courses or nonprofit educational websites, for math-focused fashion tutorials.
Remember, every fashion designer-whether working on haute couture or sustainable basics-uses math daily. By embracing these skills, you’ll unlock new creative possibilities and set yourself up for success in the dynamic world of fashion design.
References
- [1] Smart Fashion News (2025). “The Woven Wonders: How Mathematics is Shaping the Future of Sustainable Fashion.” Detailed exploration of math’s impact on sustainable fashion design and innovation.
- [2] Royal Society Publishing (2023). “Mathematics meets the fashion industry on path to product innovation.” Academic survey of mathematical models in fashion, including sustainability and digital manufacturing.
- [3] YouTube (2024). “Real-World Applications of Mathematics in Fashion – The Math Crisis.” Video overview of math in pattern making, sizing, textile design, and data-driven trend prediction.
- [4] UC Irvine (2020). “Fashion Designer.” Educational PDF highlighting math requirements and typical applications in the fashion industry.
- [5] HMH (2025). “Math Meets Fashion: How Does a Fashion Designer Use Math?” Industry insights and hands-on examples of math in fashion design.
MORE FROM savvysc.com
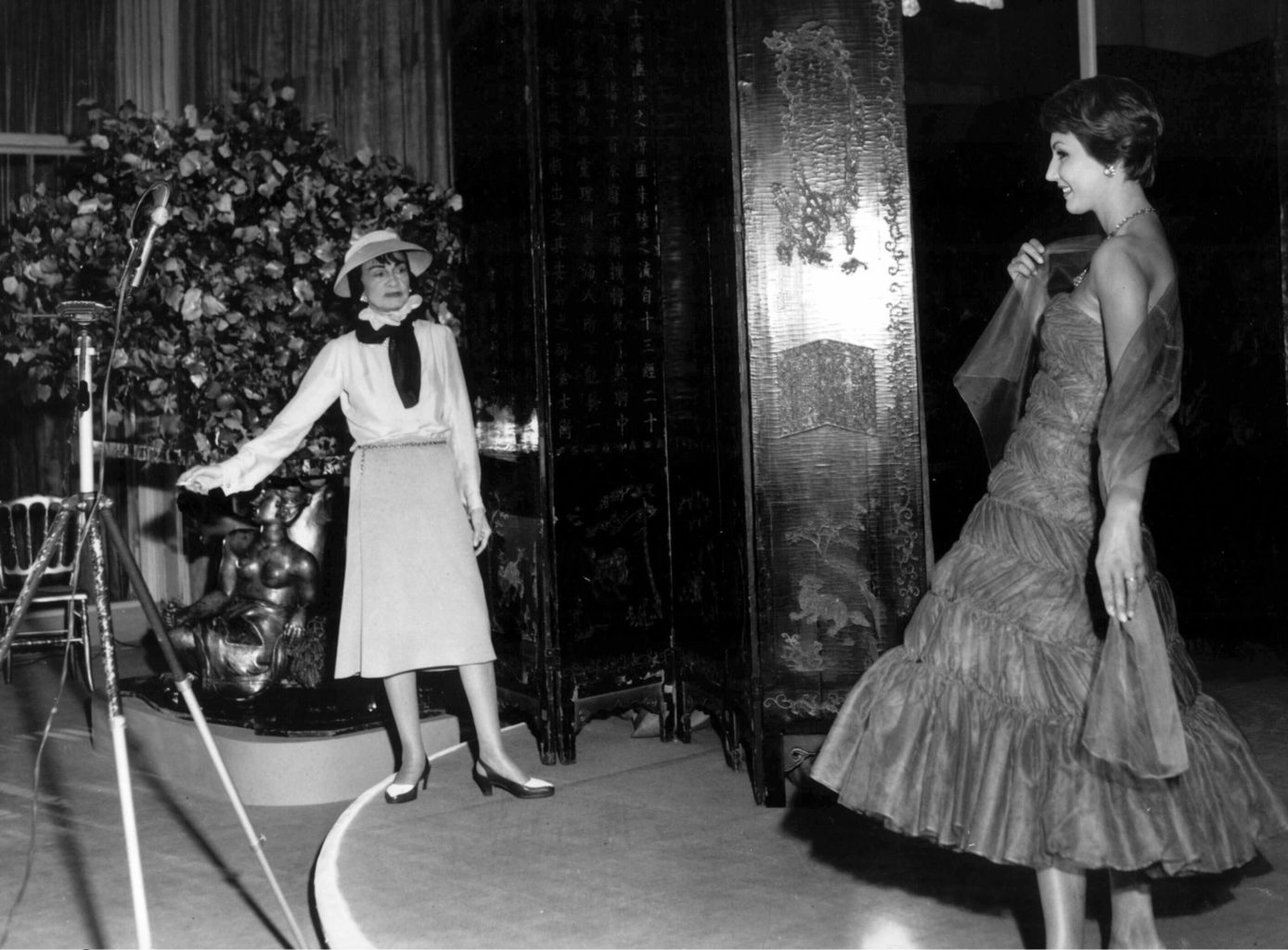
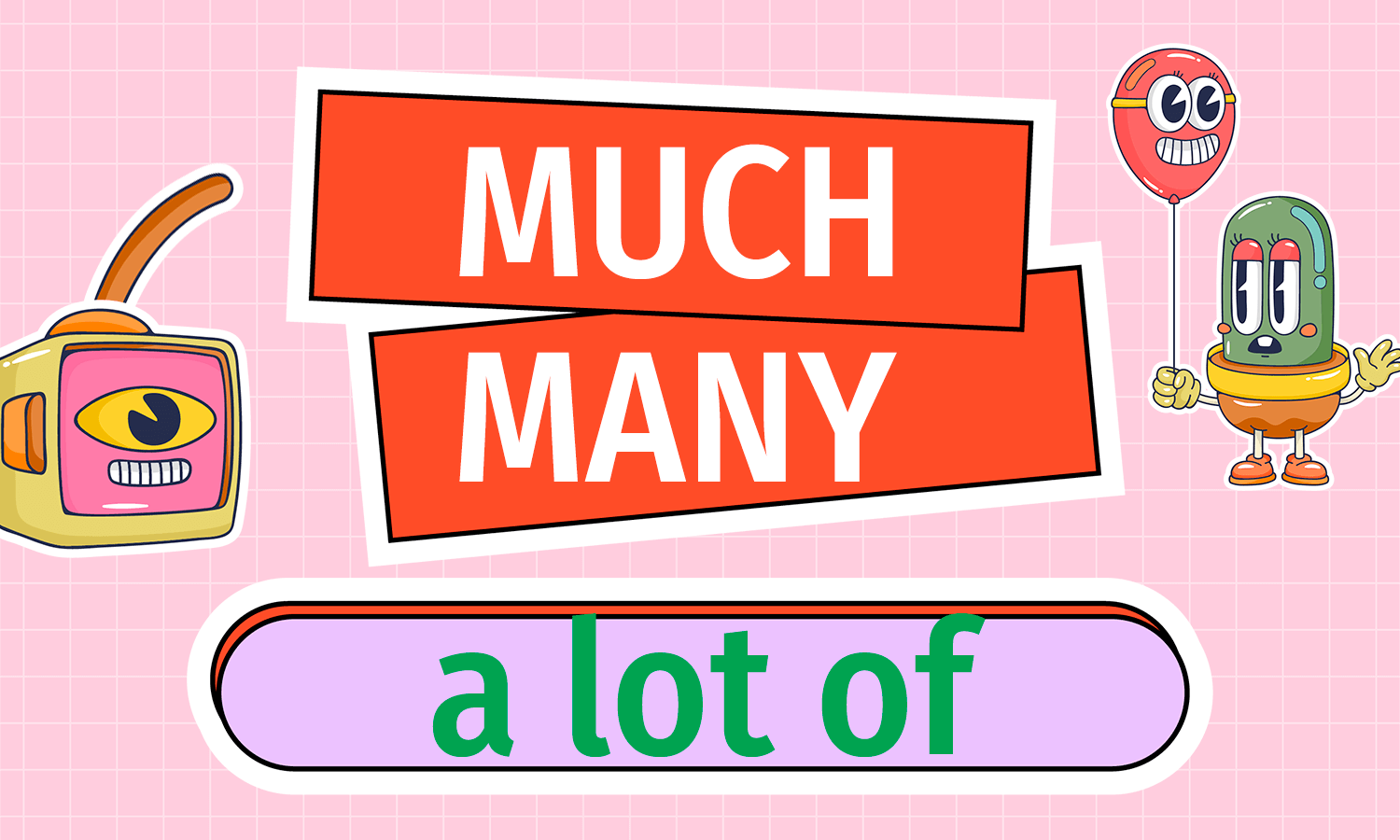
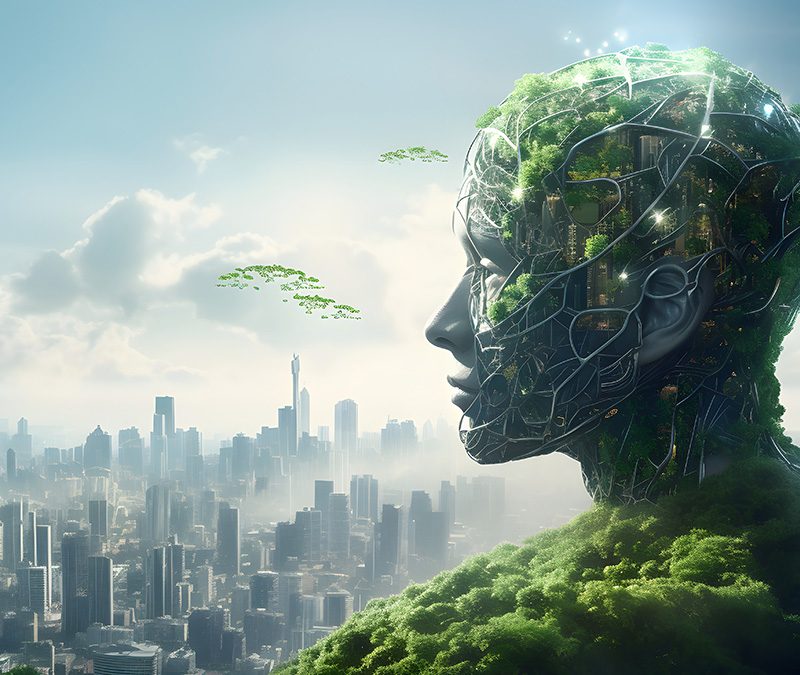
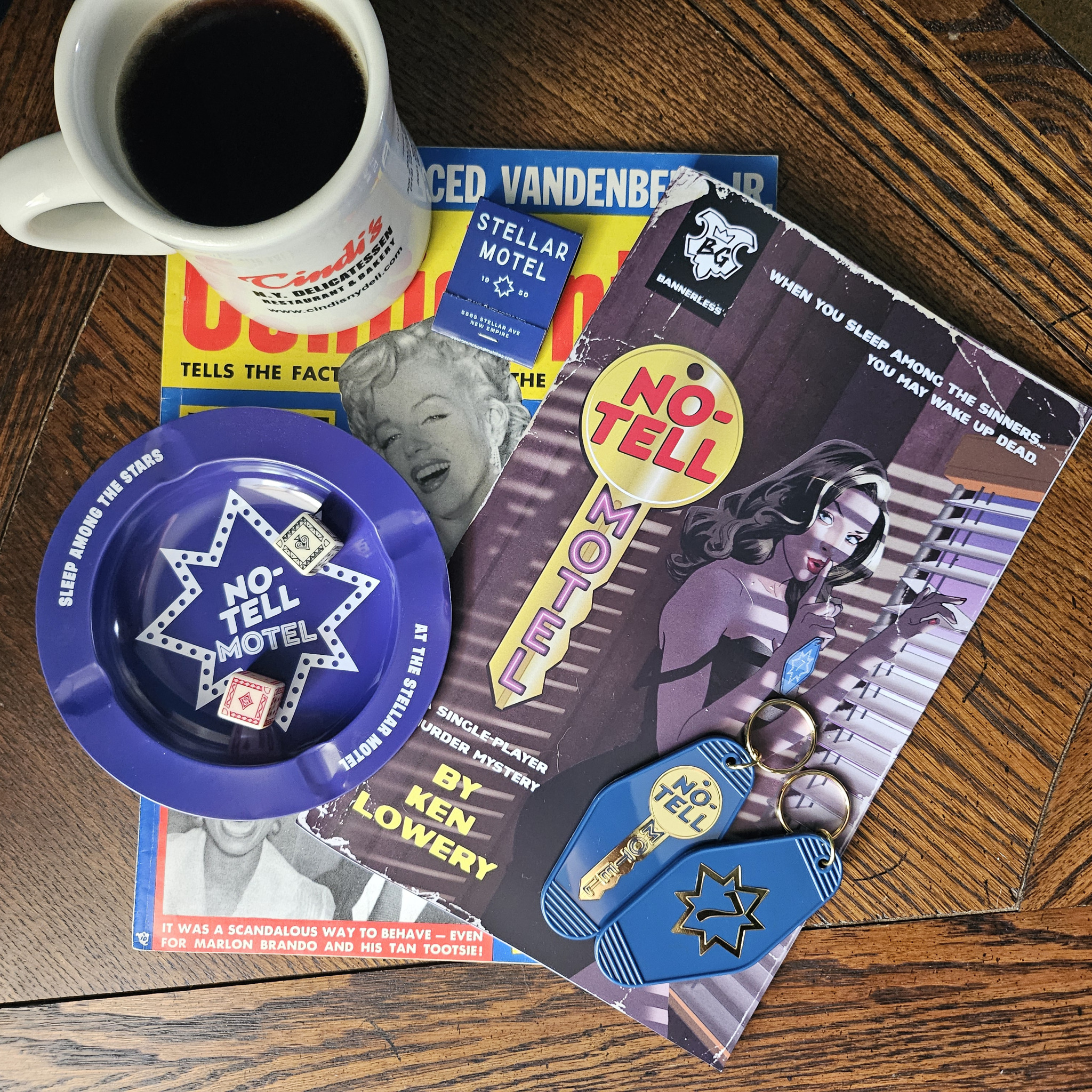
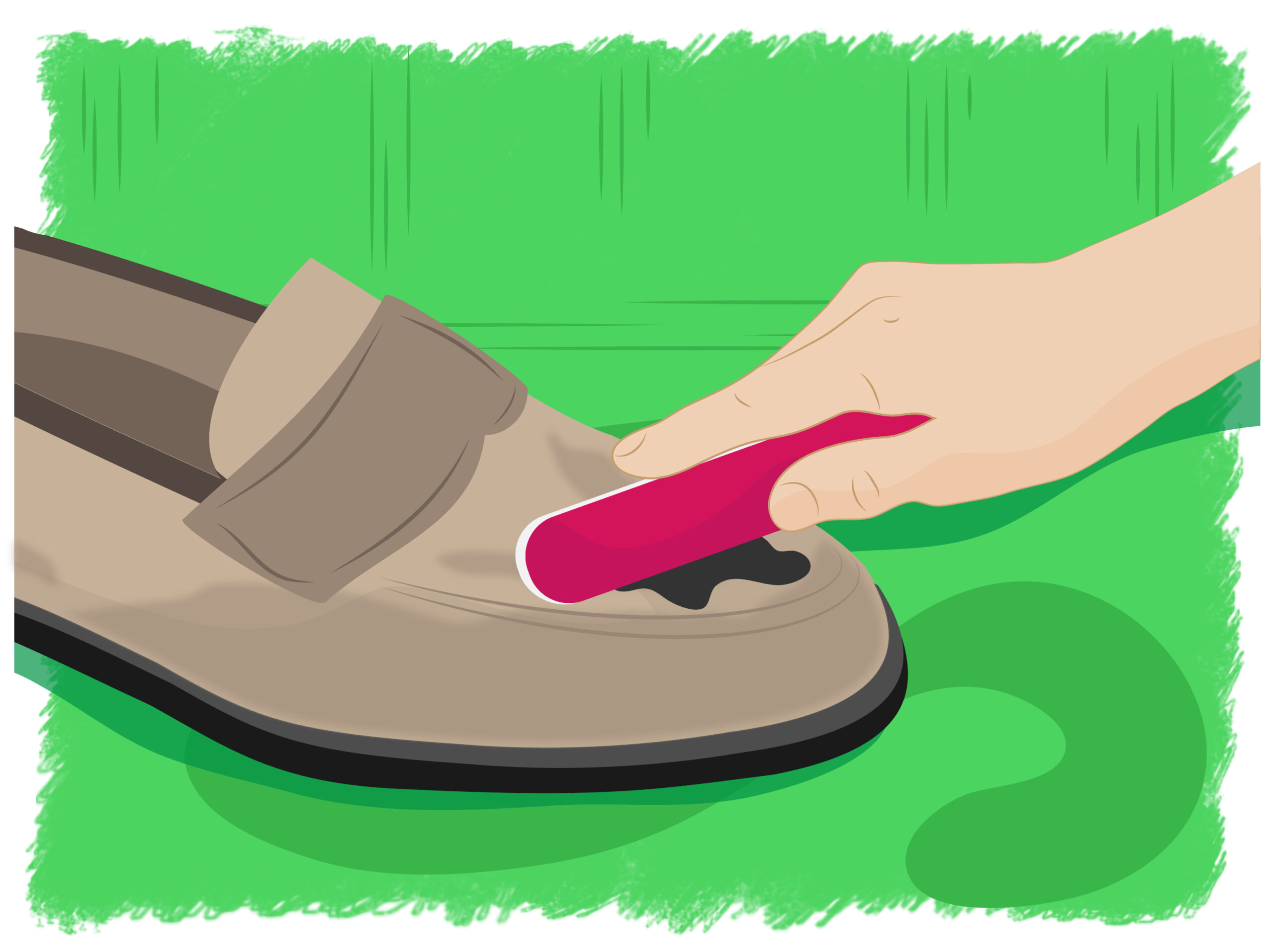

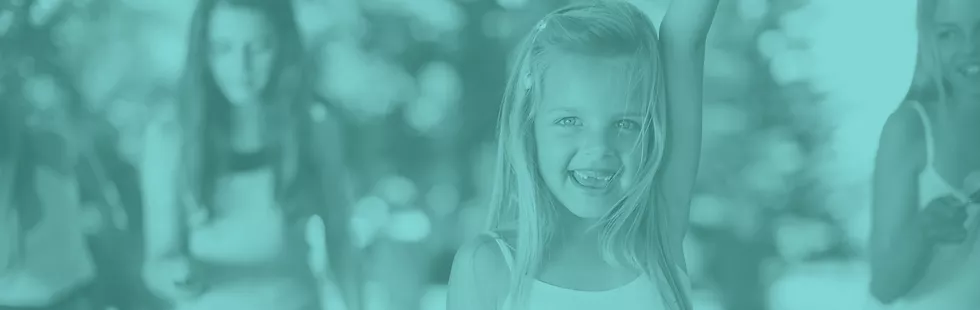
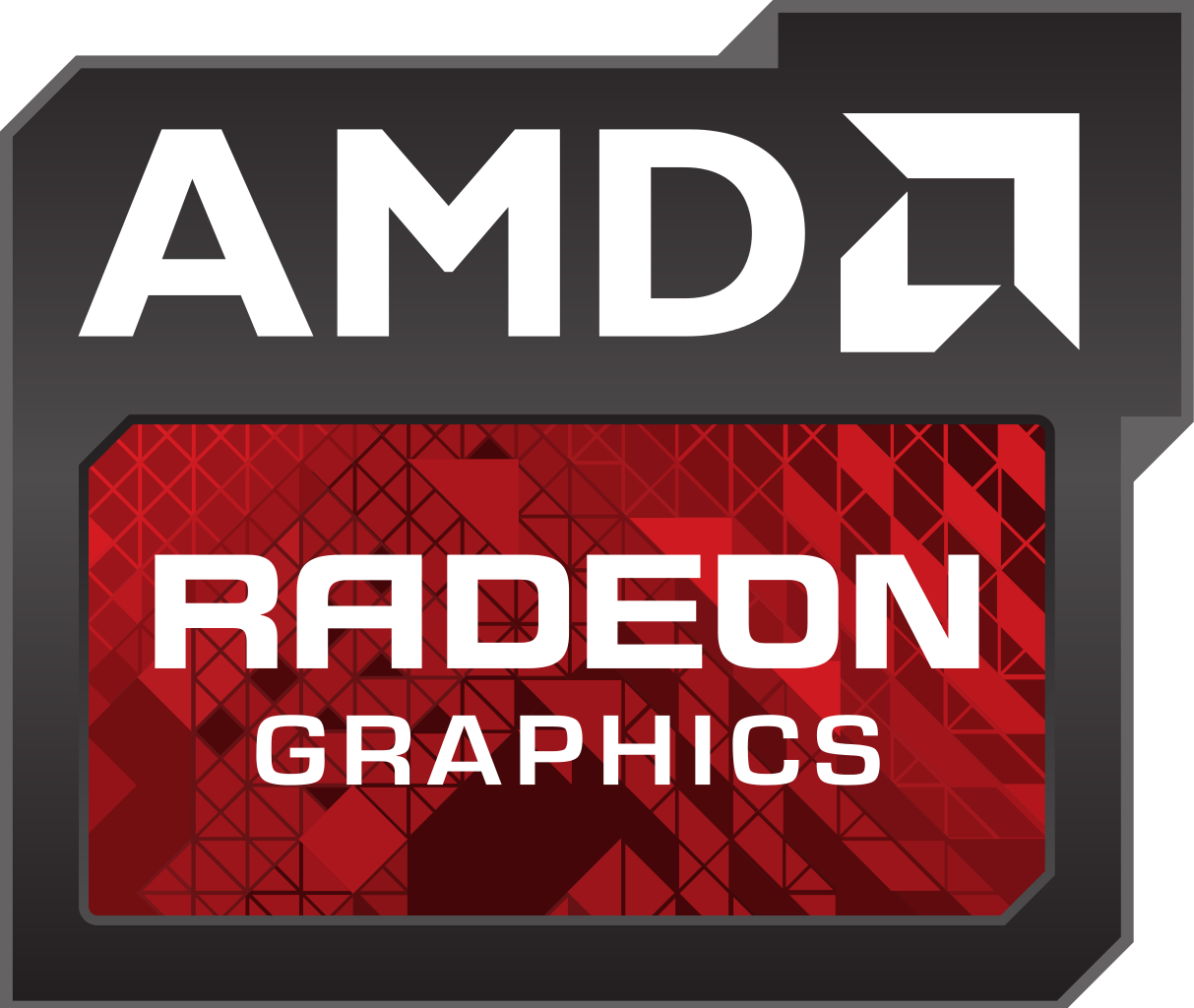

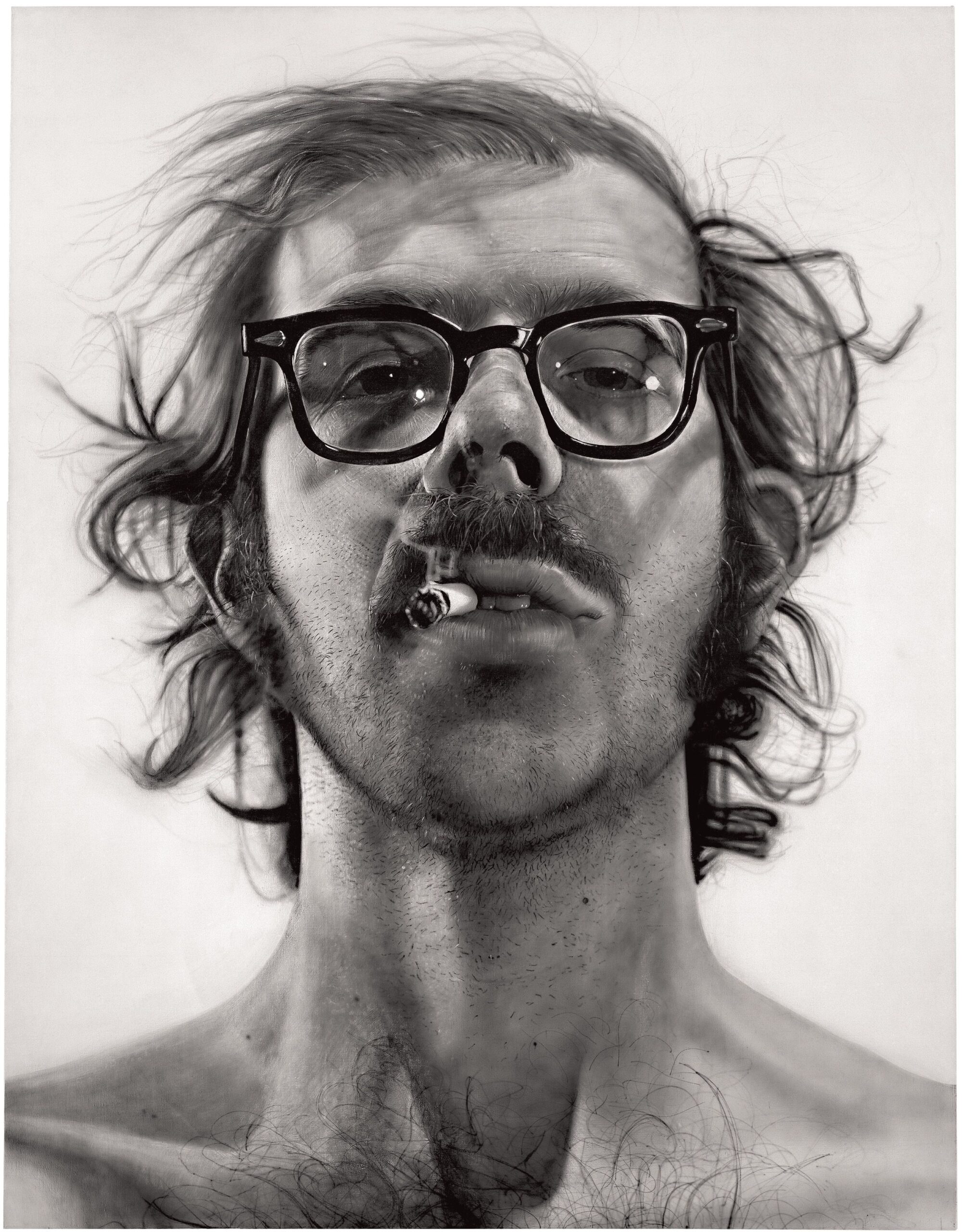
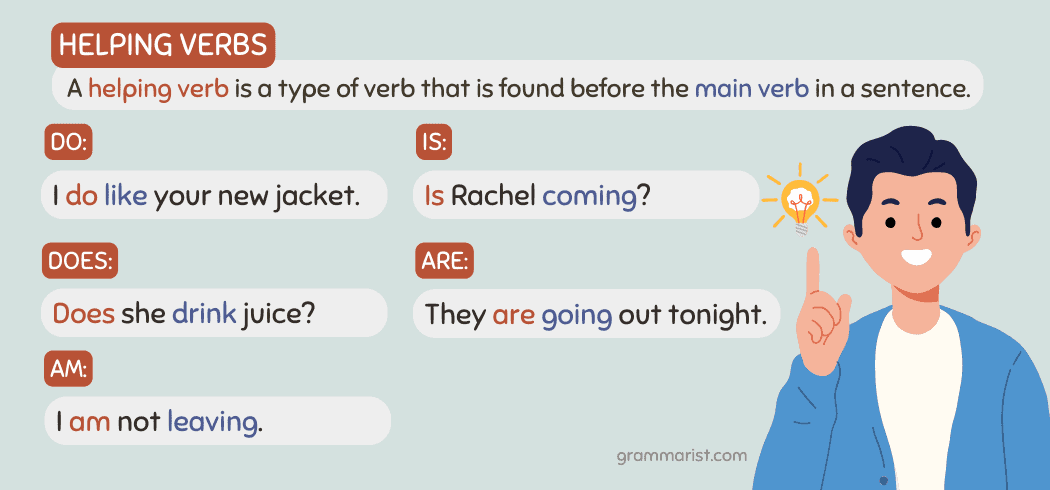
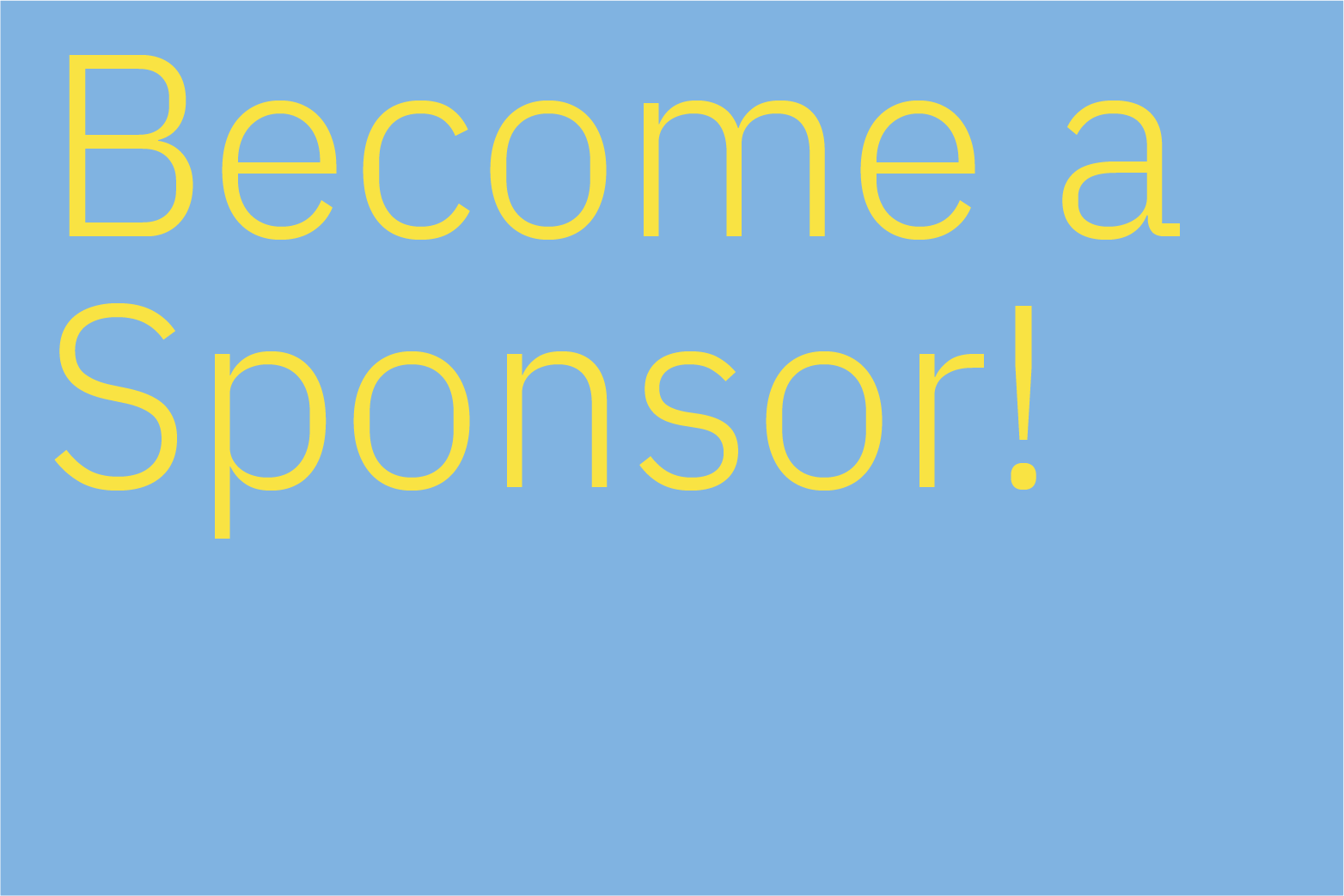